Unwinding the Enigma of Porosity in Welding: Tips for Reducing Issues and Optimizing Quality
In the elaborate world of welding, porosity stays a relentless challenge that can considerably impact the high quality and stability of bonded joints. As we dive right into the midsts of porosity in welding, uncovering the secrets to its avoidance and control will be vital for experts looking for to grasp the art of top notch weldments.
Recognizing Porosity in Welding
Porosity in welding, an usual concern run into by welders, describes the visibility of gas pockets or spaces in the bonded material, which can jeopardize the stability and high quality of the weld. These gas pockets are generally caught during the welding process as a result of numerous aspects such as incorrect protecting gas, polluted base materials, or inaccurate welding parameters. The development of porosity can damage the weld, making it prone to splitting and corrosion, ultimately causing structural failures.
Recognizing the source of porosity is crucial for welders to properly avoid its occurrence. By identifying the importance of maintaining correct gas protecting, ensuring the sanitation of base materials, and optimizing welding setups, welders can considerably reduce the chance of porosity development. Furthermore, utilizing methods like preheating the base product, employing appropriate welding techniques, and performing extensive inspections post-welding can additionally aid in decreasing porosity problems. On the whole, an extensive understanding of porosity in welding is important for welders to create premium and resilient welds.
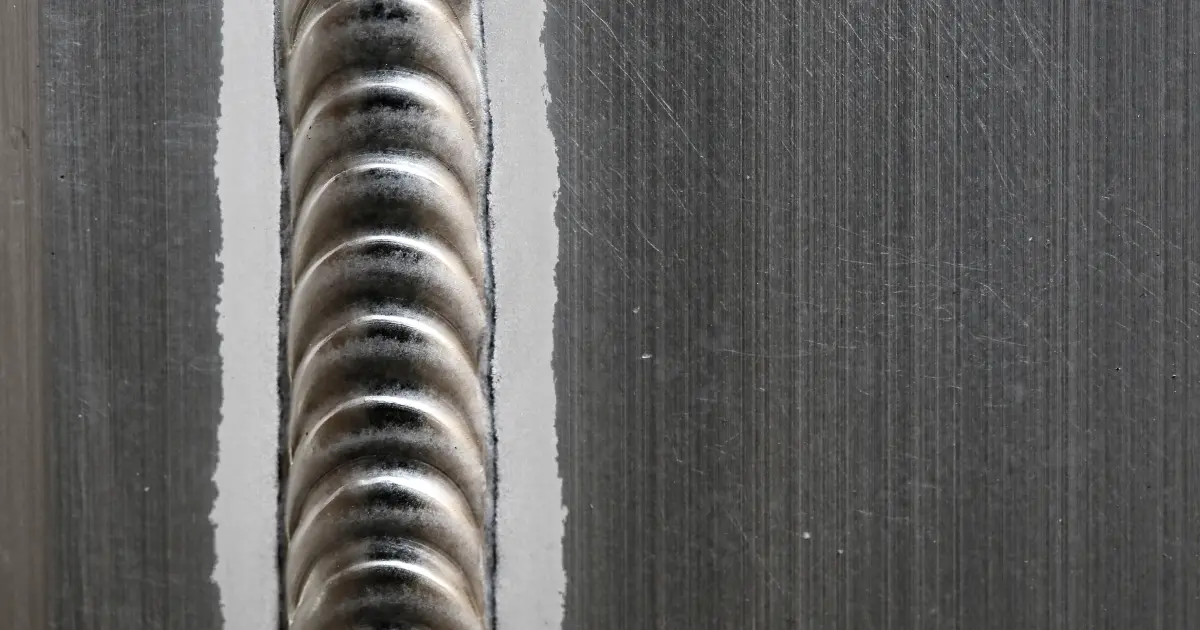
Typical Sources Of Porosity
When examining welding processes for prospective top quality issues, comprehending the typical sources of porosity is essential for maintaining weld stability and protecting against structural failings. Porosity, identified by the presence of tooth cavities or spaces in the weld steel, can dramatically compromise the mechanical homes of a bonded joint. One usual source of porosity is incorrect securing gas insurance coverage. Poor shielding gas flow prices or incorrect gas combinations can lead to climatic contamination, causing porosity development.
Additionally, welding at incorrect parameters, such as exceedingly high travel rates or currents, can generate excessive turbulence in the weld swimming pool, capturing gases and triggering porosity. By attending to these typical reasons through correct gas protecting, product preparation, and adherence to optimum welding parameters, welders can decrease porosity and enhance the top quality of their welds.
Techniques for Porosity Prevention
Executing efficient preventative steps see here is crucial in lessening the event of porosity in welding processes. One method for porosity avoidance is ensuring appropriate cleansing of the base metal before welding. Impurities such as oil, grease, corrosion, and paint can bring about porosity, so extensive cleansing making use of suitable solvents or mechanical techniques is crucial.

Another secret safety net is the option of the appropriate welding consumables. Using high-grade filler materials and shielding gases that are appropriate for the base metal and welding procedure can dramatically reduce the danger of porosity. Furthermore, keeping proper welding specifications, such as voltage, existing, take a trip rate, and gas circulation price, is essential for porosity prevention. Differing the advised settings can lead to inappropriate gas insurance coverage and insufficient blend, leading to porosity.
In addition, using correct welding strategies, such as maintaining a constant travel rate, electrode angle, and arc size, can assist prevent porosity (What is Porosity). Adequate training of welders to guarantee they comply with ideal practices and high quality control procedures is also important in reducing porosity issues in welding

Ideal Practices for Quality Welds
One trick method is maintaining correct cleanliness in the welding location. Completely cleaning up the workpiece and surrounding location prior to welding can assist mitigate these problems.
Another finest technique is to thoroughly pick the appropriate welding specifications for the specific materials being signed up with. This consists of setting the right voltage, current, travel speed, and protecting gas flow rate. Correct parameter option guarantees optimum weld penetration, fusion, and general see this website quality. In addition, using premium welding consumables, such as electrodes and filler steels, can considerably influence the final weld top quality. Buying costs consumables can cause stronger, much more durable welds with fewer issues. By following these finest techniques, welders can continually generate top quality welds that satisfy market standards and surpass client expectations.
Significance of Porosity Control
Porosity control plays an important role in ensuring the integrity and top quality of welding joints. Porosity, identified by the visibility of tooth cavities or spaces within the weld steel, can helpful resources dramatically jeopardize the mechanical residential properties and structural integrity of the weld. Too much porosity deteriorates the weld, making it more prone to breaking, corrosion, and overall failure under functional tons.
Reliable porosity control is essential for maintaining the wanted mechanical homes, such as toughness, ductility, and strength, of the welded joint. What is Porosity. By minimizing porosity, welders can improve the total quality and integrity of the weld, ensuring that it satisfies the efficiency requirements of the designated application
In addition, porosity control is important for achieving the wanted aesthetic look of the weld. Extreme porosity not just deteriorates the weld yet additionally interferes with its aesthetic allure, which can be vital in sectors where visual appeals are very important. Correct porosity control strategies, such as using the appropriate securing gas, controlling the welding specifications, and guaranteeing correct cleanliness of the base products, are vital for producing top quality welds with very little flaws.

Verdict
In verdict, porosity in welding is an usual flaw that can jeopardize the top quality of the weld. It is necessary to regulate porosity in welding to make certain the honesty and toughness of the final product.
Comments on “Comprehensive Overview: What is Porosity in Welding and How to avoid It”